OPINION
Published 16:24 IST, January 23rd 2024
On close inspection, Boeing misreads quality guide
Alaska Airlines 737 Max mishap triggered costly concerns about Boeing's manufacturing.
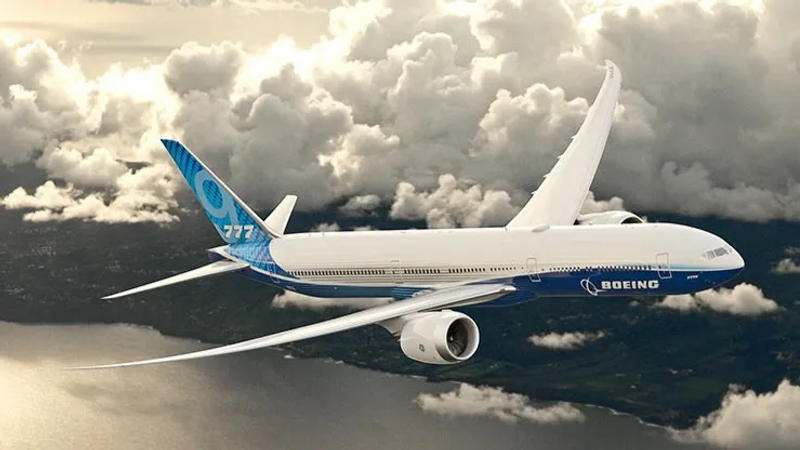
Boeing 777-9 | Image:
Boeing newsroom
- Listen to this article
- 2 min read
Advertisement
16:24 IST, January 23rd 2024